01 Planning, Design & Preconstruction
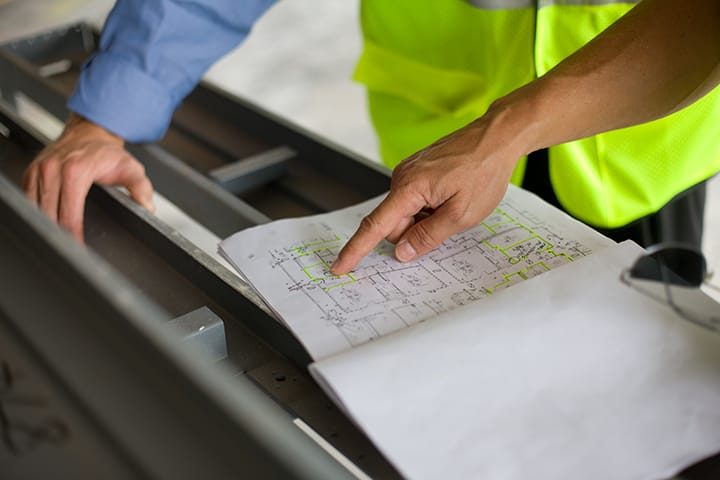
Robins & Morton’s experience shows that the most successful projects involve early collaboration among key team members during planning and design—typically the owner, architect, engineer, contractor and trade contractors. This is the genesis of the Building Forward® approach implementation on a project. Through kick-off, alignment and onboarding meetings, we establish shared expectations, common processes, and a clear management structure. Each of these activities fosters ongoing communication throughout the life of the project. Through early collaboration, teams develop a comprehensive plan and a more detailed, achievable budget.
Additionally, Robins & Morton employs a seamless process we call integrated preconstruction: a departure from the traditional idea that the preconstruction process ends when construction begins. By continuing to refine plans as a project’s design progresses, we work to meet both design and budget goals with greater efficiency.
02 Construction Phase
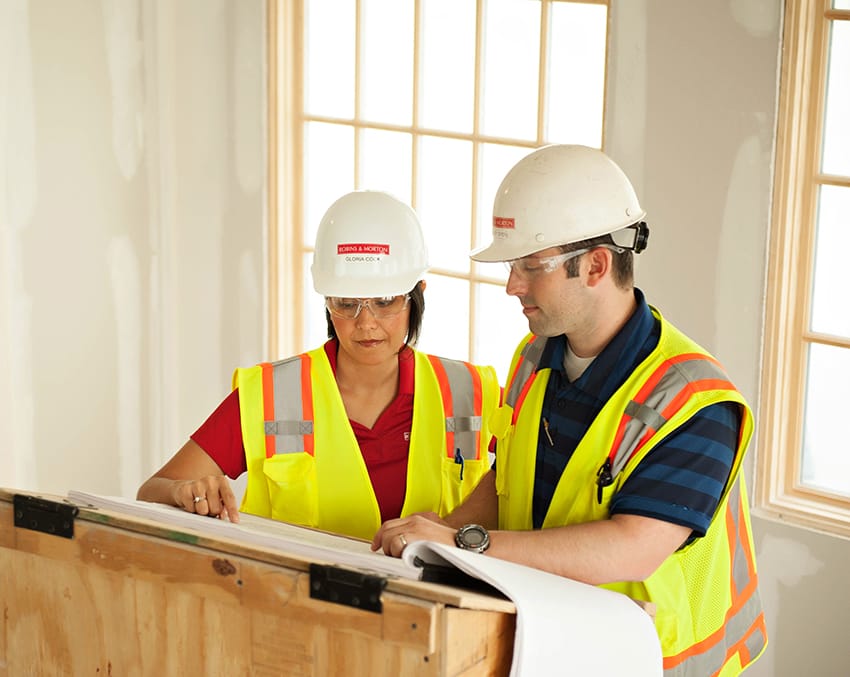
Building on the trust established during planning, design and preconstruction, the project team transitions seamlessly into construction. Beyond the essentials such as schedule management, quality control and budgeting, Robins & Morton strives to be a true partner to our clients, design teams, and trade contractors.
We do not rest on the best practices learned throughout our 75 years of operation. Because we believe that everyone’s voice brings value, our jobsites are hubs of innovation and our people continually work to find better ways to perform everyday tasks. Continuous improvement and collaboration are among core tenets of our Building Forward® approach and ultimately lead to better communication, new ways to encourage safety, the best utilization of onsite talent and greater efficiency with both time and materials.
03 Delivery Methods
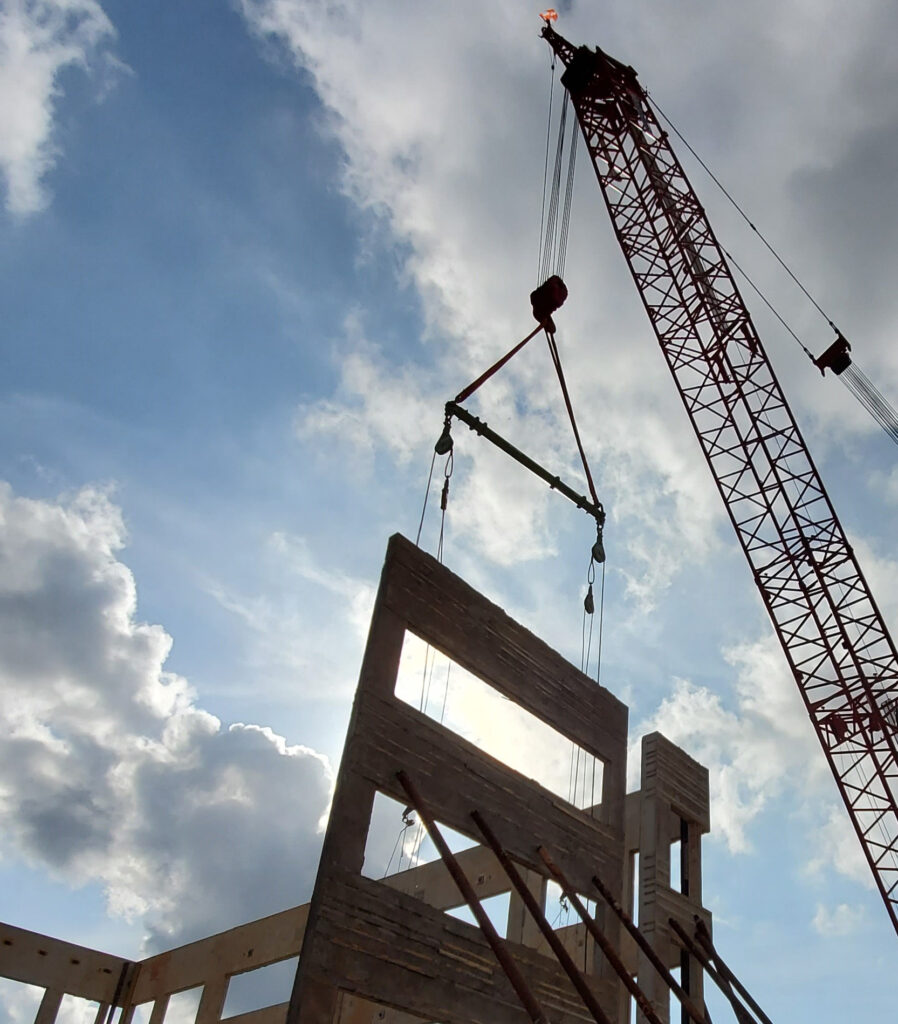
Robins & Morton has extensive experience with many delivery methods, including Construction Manager at Risk (CMAR), Design-Build (DBa), Design Assist, Integrated Project Delivery (IPD), Design-Bid-Build (DBB), and Construction Manager as Agent (CMa). We also offer program management and building assessment services.
We work with our clients to evaluate schedules, budgets, and community impact to determine the best fit for every situation. Regardless of the method chosen, we will use our Building Forward® approach to develop a custom solution for each project. We value your business and the opportunity to become your long-term partner and trusted advisor.
05 Building Envelope Services
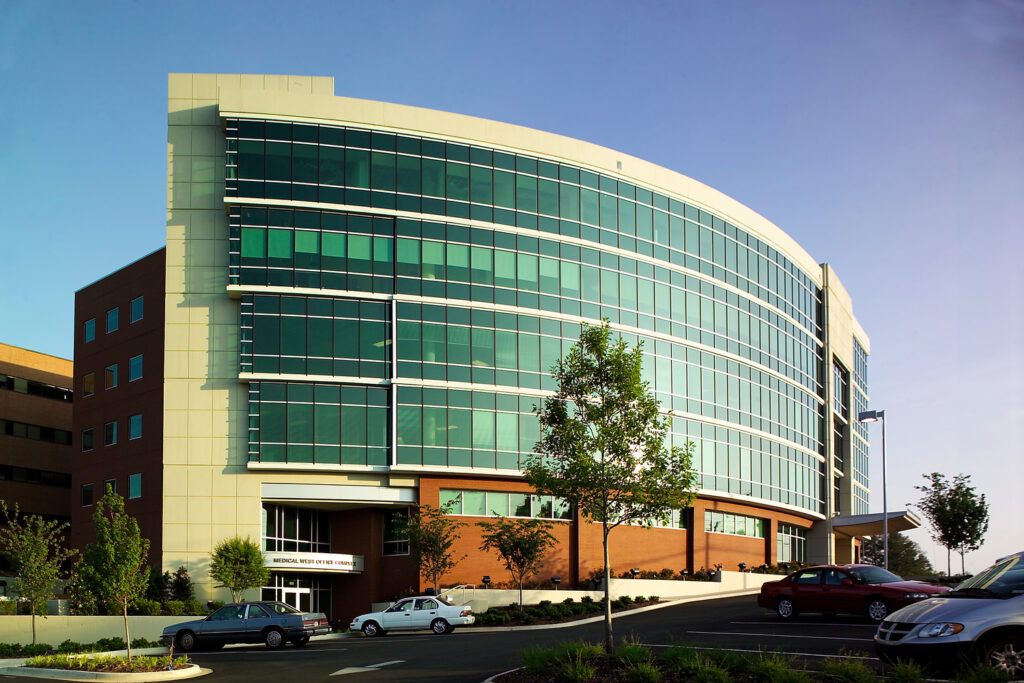
Robins & Morton’s commitment to quality extends beyond constructing buildings. Because leaks are one of the leading causes for deterioration and long-term, expensive damage, we offer building envelope assessments and practical, cost-efficient recommendations for repair.
Our in-house Building Envelope Risk Management team is led by a 40-year industry veteran, who specializes in building envelope design and quality assurance. That experience coupled with Robins & Morton’s quality management procedures bring a holistic strategy to maintain the most critical defense against potential degeneration. This proactive approach includes accurate assessments, determining a course of action for remedial work, and providing maintenance procedures to resolve deficiencies, therefore extending the service life of the building envelope and protecting your investment.
Although we are builders, we are partners first. One of our key values is to maintain a client-focus, and we recognize that it is in every organization’s best interest to avoid a continuous cycle of repairs.
To learn more about our building envelope services, reach out to envelopeservices@robinsmorton.com
06 Green Building and Environmentally Friendly Construction
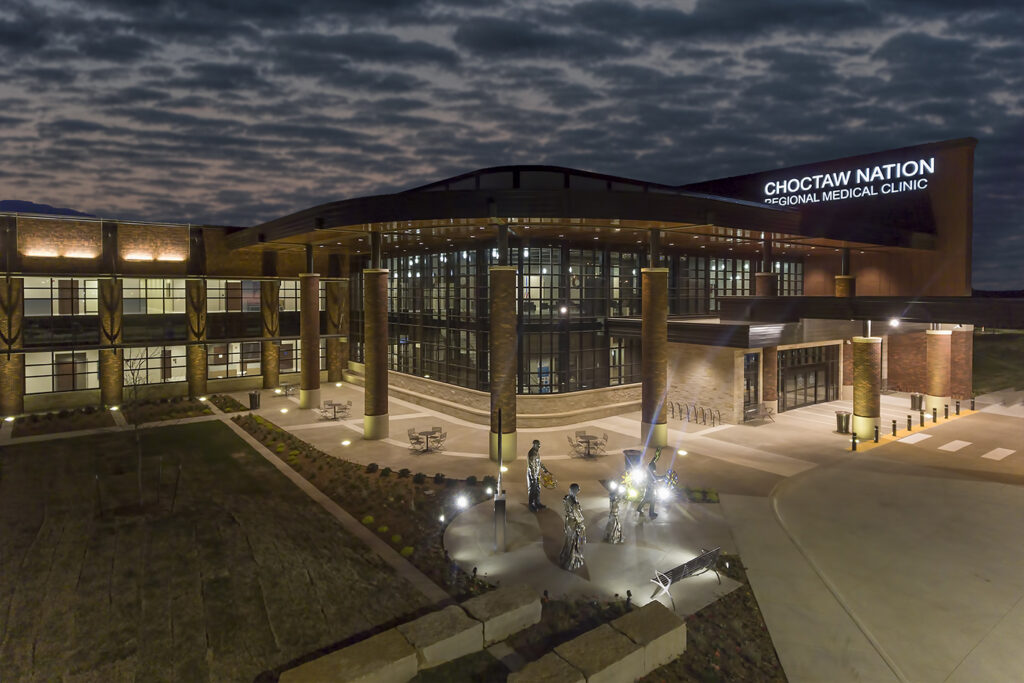
Robins & Morton strives to minimize our environmental impact and reduce our carbon footprint on every project. We tailor sustainable, knowledge-driven solutions to each client and project. Our design-assist services help clients maximize energy efficiency and minimize operational expenses while our construction procedures focus on decreasing waste and providing healthy, sustainable spaces.
Robins & Morton is a USGBC Silver Member, an Education Provider and frequently ranks among the nation’s Top 100 Green Contractors. Our more than 80 LEED Accredited Professionals, LEED Green Associates, Green Globes Professionals and ParkSmart advisors can partner with architects and other project team members to help clients achieve their sustainability goals.
On every project, including those not pursuing certification, we apply our sustainable jobsite policies and utilize environmentally responsible construction practices and materials.
Click here for our continuing education opportunities
The Robins & Morton team has genuinely been a trusted friend that goes beyond just the bricks and mortar of a construction project. On behalf of the [Encompass Health] staff and patients, we would like to thank you again for this amazing hospital building.
Elizabeth Mann,
Design and Construction Director
Encompass Health (formerly HealthSouth)
07 SmartFab®
Robins & Morton challenges our teams to innovate — to view our projects beyond the typical success metrics of budget and schedule by understanding what brings our clients the most value and considering how best to provide that value within the elements of a complex construction project. Robins & Morton’s SmartFab® approach was born of that challenge.
SmartFab® — a systematic review process to identify and implement a customized pre-assembly, modular, and prefabrication plan for each project — was developed to ensure a consistent, coordinated and comprehensive assessment of the value of these elements as well as thorough planning from design through installation. This holistic approach to prefabrication eliminates waste and improves safety, quality, schedule and budget.
Learn more about SmartFab® and the benefits realized on the Novant Health Ballantyne Medical Center project.